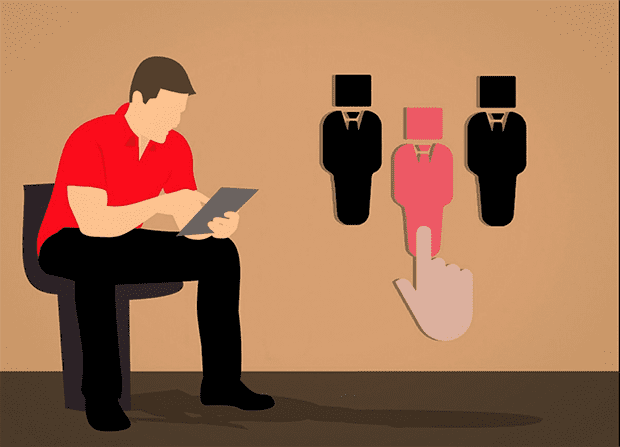
It’s no secret that the power industry workforce is aging and managers are struggling to find qualified candidates interested in filling open positions. In my April column, I referenced a…
Technical articles on all aspects of power plant operation, preventive and predictive maintenance, planned and unplanned outages
It’s no secret that the power industry workforce is aging and managers are struggling to find qualified candidates interested in filling open positions. In my April column, I referenced a…
Many combined cycle power plants are being operated as peaker plants, rather than as baseload units. That can pose a problem for economizer safety valves. Pilot-operated safety valves offer several…
Manheim, PA – Harrington Hoists, Inc. introduces their HFH Fork Truck Hook which is designed to lift and carry loads on the fork of a fork truck using a single…
The software technology, created by NarrativeWave, will enable Enel Green Power North America to better anticipate maintenance needs at its geothermal sites saving the company time and money The technology…
FLIR T840’s Integrated Color Viewfinder Simplifies Inspections Outside in Bright, Challenging Light Conditions WILSONVILLE, Ore., – FLIR Systems, Inc. (NASDAQ: FLIR) launched the FLIR T840, a new thermal camera in…
Announces Expansion into Source & Compliance Testing Services May 7, 2019, Indianapolis, Indiana: Monitoring Solutions, Incorporated is excited to announce the acquisition of Optimal Air Testing Services (“Optimal”), a Casper,…
Marc Yeston kicked off the Combustion Turbine Operations Technical Forum (CTOTF) spring conference on April 29 in St. Augustine, Florida, with a keynote presentation focused on safety, and how power…
Meeting increasing worldwide demand for wind energy depends on reliable turbine performance, and performance can significantly benefit from optimized main shaft and gearbox bearing selection. Wind turbine bearings handle enormous…
The Combustion Turbine Operations Technical Forum (CTOTF) recently announced the winners of the first CTOTF/POWER Innovation Excellence awards, which recognize outstanding performance in various combustion turbine operations categories. Among the…
Heat exchangers are vital equipment for power plant operation. Many different types of heat exchangers exist, but for applications that cannot afford cross contamination of shell-side and tube-side fluids, none…