Field Rewind with a Rotor Slot Dovetail Repair
Mechanical Dynamics & Analysis (MD&A) recently completed generator field rewind with a rotor slot dovetail repair on a customer’s GE® 650,000 KVA generator field. The work scope was performed at the customer’s direction with regards to applicable Technical Information Letters.
Incoming visual and mechanical inspections were first completed, as well as a runout inspection in the lathe which resulted in machining the turbine end journal to fix high runout in this area.
As found electrical data was then collected on the generator field by completing a 500V winding insulation “Megger” test, an AC impedance test and testing for shorts within the field winding.
After testing, the retaining rings were removed, and a full blocking inspection was performed. Significant blocking damage was found which resulted in replacing the entire blocking scheme with the MD&A recommended blocking.
Additional damage was found during wedge removal, which revealed 320 wedges with significant arc damage of about 2-3 arc marks per wedge. The wedges were successfully repaired by removing a thin amount of material from the effected wedge face. After which, they were cleaned and underwent non-destructive evaluation (NDE.)
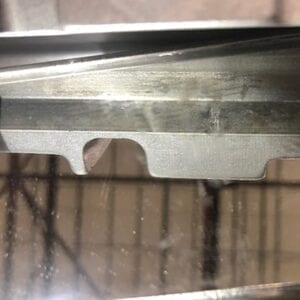
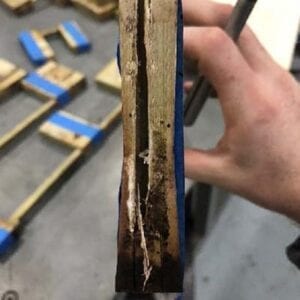
With the wedges and copper completely removed, the field was glass bead blasted and underwent NDE. HiPot testing was then performed on the inboard and outboard collector rings as well as the respective bore copper with satisfactory results.
Prior to reassembly, the copper coils were sent out for blast cleaning. The rotor body and the field body wedges were glass bead blasted. The field body was then cleaned, followed by additional NDE. The non-destructive examination revealed multiple arc marks throughout the field forging body. A formal recommendation was made to remove these indications which was accepted by the Customer.
Repairs involved machining a relief to both sides of the dovetail where the wedges meet, as well as changing the #1 slot wedges from steel to aluminum, which incorporate larger end radii. The field then underwent a second NDE which resulted in no indications.
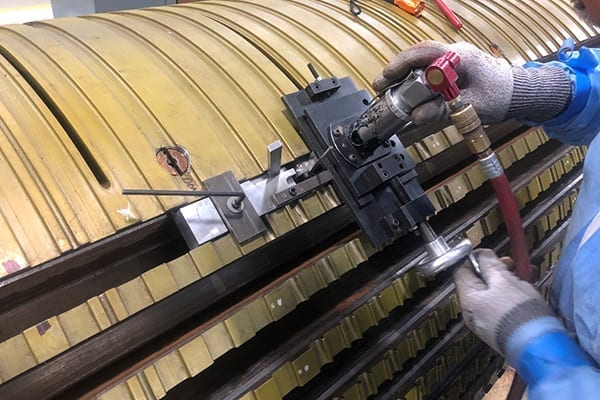
After each coil was checked and installed, they were AC Hi-Pot tested and turn-to-turn tested. A baker surge test was also completed on each coil to ensure that there were no shorts present in the winding. The turn insulation was then coated on one side with heat-cured glue, which required a bake cycle of the rotor after winding.
After the bake, a full set of electrical tests were completed including a 500V Megger test, a winding resistance test, an AC impedance test, a pole balance test, an RSO and a complete DC turn to turn test. A full set of electrical tests were also completed after the retaining ring insulation was installed and repeated after the retaining rings were installed. All results were satisfactory.
After a heat run and electrical testing were completed in our high-speed balance facility, the field was staked and painted and prepped for shipment. Before the field was shipped, a final outgoing Megger test was completed.
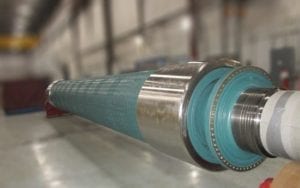
The generator field rewind was then complete with a Rotor Slot Dovetail Repair.
MD&A is a full-service OEM alternative for generator service, parts, and repairs with an over 30-year track record of successful generator stator and field repairs. We focus on delivering consistent quality and value with fast response, superior communications, and innovative solutions that meet or exceed OEM alternatives.
Call MD&A today for all your generator needs at +1 (314) 880-3000 or use our Contact form.