A new high temperature mechanical testing facility, hosted and developed by Amec Foster Wheeler in the UK, was officially opened on September 19, 2016.
This new laboratory, known as the High Temperature Facility (HTF), has been funded by the UK Government to support Generation IV reactor developments and assist with engagement in these programmes. Additionally, the new facility is able to address the mechanical behaviour of materials across the whole range of high temperature applications, including power generation and aerospace.
The project is backed by the High Temperature Facility Alliance, made up of many key UK nuclear organisations including National Nuclear Laboratory, EDF Energy, URENCO, UK Atomic Energy Authority, The Open University, Manchester University, Bristol University, Oxford University and Imperial College London. A key feature is ‘open access’, meaning that external users can undertake testing at the HTF, subject to safe operation requirements. ‘Hotel’ accommodation has been built into the facility to provide office space for visiting staff.
The official opening on 19th September 2016 was conducted by Professor Andrew Sherry, Chief Scientist at the National Nuclear Laboratory, and Greg Willetts, Vice President for Consultancy in Amec Foster Wheeler’s Clean Energy business.
Greg said: “The new laboratory and the HTF Alliance will help to re-establish the UK as a major contributor to advanced technology for new nuclear reactors and other new energy systems. The High Temperature Facility will improve our understanding about how materials perform at high temperatures, which is vital in the development of new technologies.”
The new temperature controlled laboratory is equipped with the latest equipment for creep, fatigue and fracture testing. Although a temperature of 1000°C can be obtained for most tests in the HTF, this can be significantly exceeded for some applications by using radio frequency heating. Instrumentation provides a good understanding of the materials behaviour associated with the various deformation processes, including digital image correlation for 3D full-field strain mapping, crack detection techniques like AC and DC potential difference monitoring, and acoustic emission.
This equipment will enable users to determine the safe operating life of new and existing materials for the full range of service temperatures and loads, supporting plant life extensions and new build design requirements. The ability to understand material behaviour at a fundamental level permits the construction of the best models and simulations, which underpin many structural life predictions.
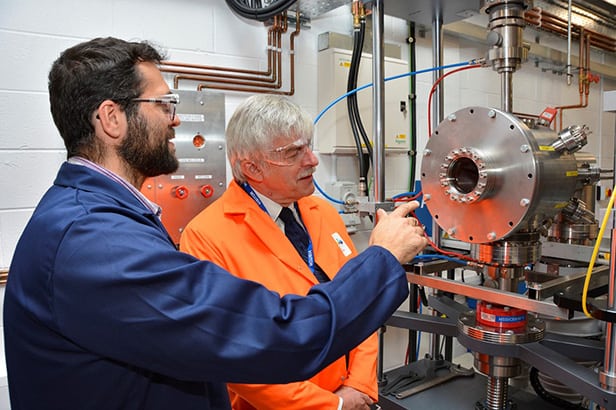
The HTF can simulate relevant environments for differing applications. This aspect of mechanical testing is becoming more widely recognised as important for correctly simulating service conditions in a range of industries, especially as plant operating temperatures increase to take advantage of improved thermal efficiencies. Initially therefore, the HTF is developing a capability to test mechanically in pressurised gaseous environments, such as CO2 and helium, in support of the UK’s advanced gas-cooled reactors (AGRs) and Generation IV high temperature reactor concepts. This pressurised gas example also highlights the potential for cross-sector collaboration because environmental conditions in some gas turbines are similar.
The HTF’s capabilities are also applicable to other Generation IV reactor environments including liquid sodium and lead (and lead-bismuth) and supercritical water, including the ability to balance these potentially aggressive environments by testing under vacuum conditions (or inert gas) to establish the level of environmental impact on material deformation or fracture behaviour.
Environmental mechanical testing can be vital for a range of different behaviours affecting component life, including fatigue crack initiation, fatigue crack growth and creep crack growth. The first of these is important for the design of new plant, whilst all three can be crucial for plant life extension and determining inspection periods across the whole range of industrial sectors. The major challenges with mechanical testing in relevant environments are often around the operation of suitable instrumentation, and the HTF has been designed with this in mind.
The stage is set for the HTF and the alliance members to contribute significantly to a whole range of structural integrity issues associated with high temperature materials, so Amec Foster Wheeler is actively seeking opportunities to collaborate and work with organisations throughout the world.
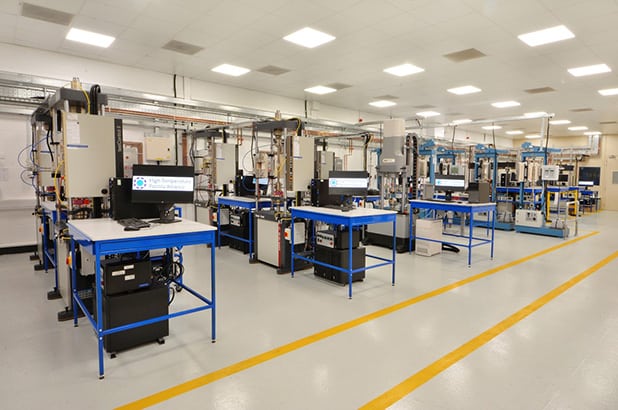
Contact
Dr Andrew Wisbey, Amec Foster Wheeler