Noted management consultant Peter Drucker once wrote that "an established company, which, in an age demanding innovation, is not able to innovate, is doomed to decline and extinction." Some say electric utilities were the inspiration for Drucker’s comment. Because its main product is a both a service and a commodity, the electric power industry doesn’t value innovation as highly as, say, the communications or computer software industries, where billion-dollar bets on the success of a new product are routine. Most of today’s top utility executives were attracted to the business by its stability and predictability—not because they were looking for a chance to compete at the retail level.
Regulation discourages utilities from nurturing or promoting innovation. For those that tried to buy their way into growth industries a decade ago, the results were not always what they expected. Diversification doesn’t always lead to success, and many utilities were bloodied while trying to compete in businesses for which they were inadequately trained and equipped. Today, the pendulum has swung back to the other side, and "back to basics"—improve reliability, reduce costs, and improve customer service—has become more than one utility’s corporate mantra. It’s tough being entrepreneurial when technical accomplishments are focused on cost savings rather than R&D and new products.
There are exceptions to every rule, however, and those exceptions are what make for interesting case studies—like this one. In June, the Edison Electric Institute selected Xcel Energy as one of two recipients of its 2006 Edison Award in recognition of the company’s "commitment to cutting-edge technological innovation." The award is highly coveted by utility executives, and the competition each year is stiff. The final selection is made by a team of former C-level utility executives who have the unenviable task of finding the best among the many deserving nominees.
Path to profits
Wall Street is looking for key differentiators among what must appear to be many similar vertical businesses operating in the electric utility sector. Growth in earnings per share will continue to rule, but growth can’t be achieved simply by cutting operating costs. Some utilities are looking to grow through mergers and acquisitions. Others attempt to build a high-performing organization from within, by weaving technology into the fabric of the corporation and by creating a culture that values continuous improvement.
Which approach will generate the bigger return on each shareholder investment dollar remains to be seen. But my bet is on companies that build a firm foundation for future growth by investing in their technology and organizational infrastructures.
Joining forces
In December 2003, Xcel Energy launched an initiative to determine if leveraging information technology could improve its business operations, cost structure, delivery reliability, and customer satisfaction. As an industry leader, Xcel is choosing to share the results of this initiative with its peers. Xcel Energy’s belief that collaboration is the key to innovation was put to the test when the company first brought together its leading technology suppliers—IBM, Indus International, and Itron, among others—to form Utility Innovations. (To better understand the initiative and the role of the partners, visit www. xcelenergy.com and click on Utility Innovations, under the Newsroom tab.)
For Xcel, the first step was to get its suppliers in the same room and convince them that collaborating to find permanent solutions to vexing problems would benefit them as much as it would their host and customer. After much conversation and outside-the-box thinking, the suppliers began to grasp the possibilities of partnerships among vendors. Utility Innovations (UI) serves as the framework for a new kind of relationship, one in which IT providers work together to test and validate new technologies and integrate existing technologies in novel ways (see box).
Initiatives proposed by Xcel employees or UI Technology Partners (either individually or in concert) are first approved by the UI team and then presented to an internal executive board or UI’s Strategic Advisory Board for implementation. If implementation requires different expertise, new Technology Partners may be invited to join UI. Any competing proposals also are reviewed, and whoever presents the best business case is named the winner and invited to negotiate a contract with Xcel Energy.
The completion of a series of successful pilot projects during 2004 led to the 2005 establishment of Utility Innovations as a formal business unit, headed by an executive director appointed by Xcel Energy’s CEO on a one-year rotating basis. Since then, many more technology providers have joined the initial group of partners to bring the best solutions possible to the table. This year’s new members include ABB (www.abb.com), Meridium Inc. (www.meridium.com), SmartSignal Corp. (www.smartsignal.com), GE (www.gepower.com), Zolo Technologies (www.zolotech), and the U.S. National Renewable Energy Laboratory.
"Utility Innovations is leveraging this unique technology partnership to make our business processes industry leaders, increase customer satisfaction, and provide reliable power at a low cost," said Xcel Energy Vice President of Customer & Enterprise Solutions and Chief Administrative Officer Ray Gogel. "Our company is providing the canvas on which technology providers can work with us to create a new, standard-setting picture for the electric utility industry."
Making the team
One key project completed earlier this year was sponsored in 2005 by a team from Meridium and SmartSignal as the companies" "audition" to join UI. The project aimed to develop a predictive maintenance (PM) program for power plants that combines real-time and PM techniques to optimize maintenance activities, thereby reducing O&M costs.
Units 3 and 4 of Xcel Energy’s 715-MW, coal-fired Cherokee Station north of downtown Denver (Figure 1) were selected to host the pilot PM project, which ran from mid-September 2005 through February 2006. The pilot project targeted Xcel’s Energy Supply business unit, which for several years had used data sources such as MRO Software’s Maximo and plant distributed control system historians to help predict equipment failures and improve plant performance. However, the process of integrating the data sets proved to be so complex and time-consuming that their value was not being fully realized.
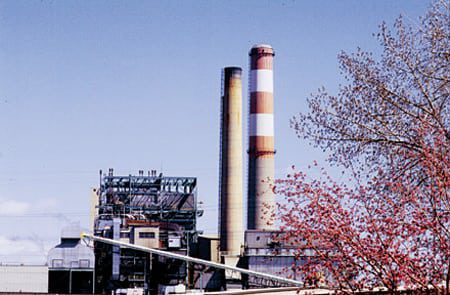
1. Pilot testing. Cherokee Station near downtown Denver was the site used to determine how well software tools could predict equipment failures and refine maintenance intervals. Courtesy: Xcel Energy
The Meridium-SmartSignal team accepted the challenge of finding a better way to optimize O&M strategies. Meridium’s Asset Performance Management System (APMS) integrates information and analysis to identify and mitigate recurring failures by determining the optimal mix of condition-based, time-based, and run-to-failure activities. SmartSignal brought to the table its analytic tools, which identify possible but unpredictable failures. Combining the capabilities of software from three companies—MRO Software, Meridium, and SmartSignal—enabled Xcel Energy to minimize the damage caused by predictable and unpredictable failures alike (Figure 2).
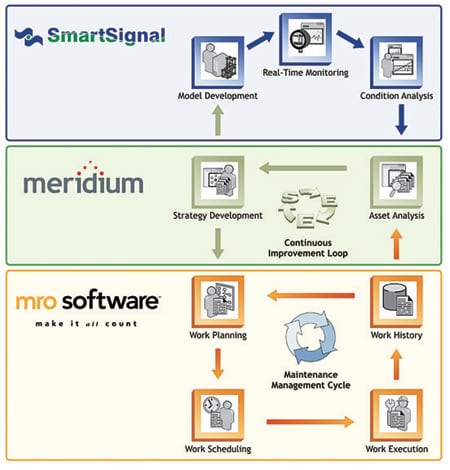
2. Roadmap to success. The Cherokee Station pilot project integrated software tools from Meridium and SmartSignal to optimize plant maintenance strategies. Courtesy: Meridium
The historian data were modeled by SmartSignal for advanced issue recognition and condition-based analysis. The Maximo data were organized and analyzed around equipment descriptions, conditions, locations, and historical work performed using Meridium software. Feeding SmartSignal data into the Meridium software increases the confidence level for prediction accuracy over that of independent analysis while enhancing the accuracy and value of the analysis.
Taking the challenge
Several test cases were examined at Cherokee Station. They spanned several layers of complexity, beginning with a simple example of how data integration works at the equipment level and then moving to more complex analyses at the system level.
Optimizing PM. As part of the test, software from SmartSignal and Meridium was used to predict the longevity of the seals of Boiler Feed Pump 3A. The current probability of seal failure was determined to be 18.8%. Based on historical performance data and assuming normal operating conditions, the software calculated that the probability of failure would rise to 54.6% in 200 days. Although the seals are expected to fail every 318 days, by taking into account the differences between unplanned and planned maintenance costs, the software determined that the optimal PM interval for seal work is 274 days. A key number like that can be used to prioritize critical tasks during planned outages for scheduled maintenance.
Equipment performance data from SmartSignal were used to determine if the seals of pump 3A were healthy enough at the 274-day point to further extend the PM interval. In this case, new mean-time-between-failures statistics were generated to refine the optimum PM time. Additional information from SmartSignal was combined with Meridium’s reliability-centered maintenance analysis to reduce time to repair and to determine equipment criticality and appropriate overhaul intervals.
Minimizing failure costs. The same boiler feed pump was analyzed as part of a system model that also included pumps 3B and 3C. The model assumes that two pumps run simultaneously, with the third serving as a spare to ensure that Unit 3 can always operate at full load. In calculating predictions for the next 1,000 days, the SmartSignal and Meridium software determined that total failure-related costs for the period would be approximately $100,000. A more-detailed analysis of the data indicated that both the 3B and 3C pumps could be expected to fail during the period, but not at the same time.
By predicting failures that can be expected over a fixed period, the system model improves operational planning. For example, $100,000 in failure costs for this system are more than justified by the revenue generated during a 1,000-day run of a generating unit. Alternatively, the analysis may suggest performing critical tasks during shorter outages during off-peak windows as a way to minimize costs while maximizing generation. When this system model is evaluated in the context of a larger system model (for the entire four-unit Cherokee plant, for instance), it may even become feasible to postpone some scheduled outages.
Making output more predictable. The system model also defines the probability of maintaining a desired generation level during any given month. A Weibull analysis of data on Cherokee Unit 4 from January 2003 to December 2004 indicated that the unit’s median monthly generation is 192,802 MWh. Building on this analysis, the software tools were used to optimize planned maintenance and reduce system operating risk. Using historical generation data, the condition of the equipment and system can be used to predict future generation based on reliability improvements made at the plant.
Improving operations. The pilot PM project developed dynamic views of all assets in Units 3 and 4. For example, the view of an asset called "Cherokee 3D Mill" now includes the mill’s location, work histories, SmartSignal Watch Lists, condition results, previously performed tasks, documented recommendations, and reliability analyses performed on it. The system also can document and manage inspections, calibrations, thickness measurements, and recommendations. At Cherokee Station, Meridium adapted its APMS tools to respond to SmartSignal alerts. Providing a single view of an asset facilitates rapid analysis by plant operators.
Reducing unplanned downtime. During the pilot, generation availability data, Maximo data, and SmartSignal data were analyzed together to further facilitate operator analysis. With all data residing in one integrated system, alerts from SmartSignal can be verified and acted upon more rapidly. Other benefits include the potential for maximizing reliability through root-cause and failure-and-effect analyses. Finally, the integration allows a user to not only measure confidence levels of calculation results but also to more confidently make decisions to defer maintenance. The bottom line—as is usually the case when technology is leveraged in a power plant—is a reduction of unplanned downtime.
Boosting employee productivity. When O&M analysts work off-site, they might be unaware of the external factors that may be creating condition-based alarms. The software integration achieved by the pilot PM program created a more efficient and sustainable system for analyzing problems.
For example, remote analysts were capable of being informed—at the beginning of their shift—of all activities planned for the plant for the day that could produce an alarm. They could obtain that information as easily as by querying a database listing all calibrations due or overdue for monitored equipment. Examples of calibration tasks scheduled for the Cherokee plant were included in the pilot demonstration. A similar query could give the analyst a view of all work activities scheduled for that or any other day, week, or month.
When there is a new alarm, an analyst may want to verify maintenance work in progress on the machine being analyzed. This was demonstrated at Cherokee by having an analyst select a query that returned the Watch List Log, which includes links to associated work histories on the same machine that occurred within seven days of the SmartSignal log date.
When more detailed history is needed, the Meridium application enables a hyperlink to multiple options that include the Watch List Log detail, the asset data sheet, and the work order associated with that entry. The ability to see all events and information related to a specific asset and an entire system, and to monitor work performed on a remote plant, dramatically improves employee productivity.
Final results
By hosting the pilot PM project, Xcel Energy learned that it could potentially save $1 million at Cherokee Station by reducing maintenance and fuel expenses and maximizing generation revenue. That the pilot project was able to draw that conclusion in just a few months made it a complete success.
"When you think about ‘utility innovations,’ those are two words you don’t normally put together in the same sentence, said Xcel Energy’s Chairman, President, and CEO Dick Kelly in his Edison Award acceptant speech. "But I think in the future you’ll look to companies like Xcel Energy, and whether you’re addressing environmental challenges, customer service issues, or whatever it may be, hopefully you’ll see innovative techniques that enhance the business and improve its day-to-day operations."