Chromium-molybdenum (chrome-moly) pipe has become a standard in the power generation industry, not only because of its corrosion resistance and high-temperature strength, but also for its cost-effectiveness. In many applications, it is a viable alternative to a more costly stainless steel pipe.
Choosing filler metals to weld chrome-moly pipe requires the same considerations as choosing any material: Match the chemical and mechanical properties in a way that yields the strongest, safest, and longest-lasting welds. Specific low-alloy shielded metal arc welding (SMAW) electrodes and flux-cored (FCAW) wires do just that. They provide the low-carbon, low-hydrogen properties that prevent welds from corroding and/or cracking on critical piping applications, as well as the necessary strength to withstand high pressure and temperatures. It just takes a little know-how to choose the right electrode for the job.
Mind your “Ps”
To select low-alloy filler metals, it is first important to understand chrome-moly pipe itself. Among the more common grades are P11, P21, P22, P91, and P92, some of which can withstand service temperatures over 1,112F and have wall thicknesses ranging from 1/8-inch to 8 inches. The amount of chrome, molybdenum, or other alloying elements determines the assigned grade of chrome-moly. These particular grades contain a range of 1¼% to 9% chrome and ½% to 1% molybdenum. Those containing more chrome provide the most corrosion and temperature resistance. Not surprisingly, the amount of chrome is also a determining factor in filler metal selection.
When welding chrome-moly pipe, regardless of the grade and/or the filler metal being used, it is important to maintain specific preheat and interpass temperatures. Consistent temperatures help conserve strength and crack resistance under extreme service conditions. Recommended preheat temperatures range from 250F to 400F, according to the wall thickness (Figure 1).
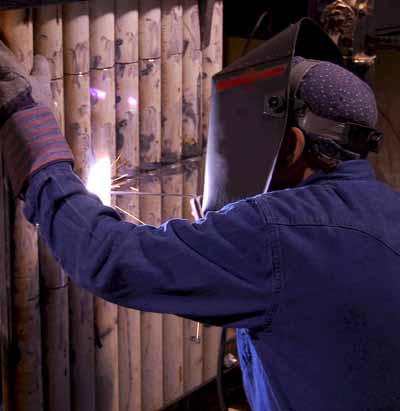
1. A welder must preheat the wall and replacement boiler wall pipes before tacking and final welding. Courtesy: Hobart Brothers
Per American Welding Society (AWS) code D10.8-96, “Recommended Practices for Welding of Chromium-Molybdenum Steel Piping and Tubing,” preheating practices should always be observed, even before tack welding. It is especially important to preheat prior to repairing P21 and above-grade chrome-moly pipe that has been in service, as it may experience temper embrittlement or ductility loss. This can occur when the pipe has been exposed to temperatures above 850F for an extended period of time (see AWS D10.8-96, 5.1 and 7.2).
Maintaining interpass temperatures is also important. A range of 350F to 600F is typical, depending on the grade of chrome-moly and its thickness but also, and most importantly, upon the required welding procedure.
Postweld heat treating (PWHT) or stress relieving is also recommended. PWHT requirements are typically 1,150F to 1,400 F for one hour. PWHT helps rid the weld of hydrogen that may have been picked up from the filler metal, the base metal, or the atmosphere, and can help minimize the chances of cracking. Most low-alloy filler metals designed for chrome-moly applications will also provide recommended stress-relieving temperatures and duration on the label or spec sheet (Figure 2).
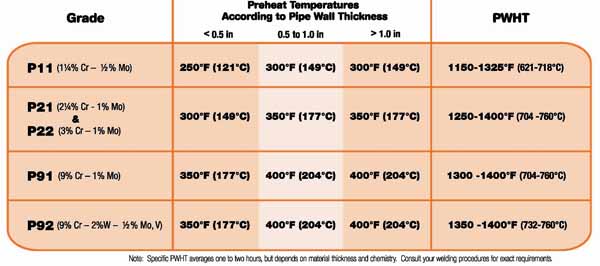
2. Recommended preheat and postweld heat treating temperature for welding chrome-moly pipe. Source: Hobart Brothers.
No Reason to Get Stuck
Low-alloy SMAW electrodes are your best choice for chrome-moly pipe welding repairs because they are easily portable (they do not require shielding gas). They can also reach into the small physical confines of existing chrome-moly piping systems.
As a rule, low-alloy stick electrodes designed for welding chrome-moly feature low hydrogen levels, low spatter, fast freezing, easy-to-remove slag, and good bead wash and tie-in, all of which are designed to make welding repairs fast and trouble-free. To obtain these characteristics, be certain to clean the pipe prior to weld repairs. Chrome-moly often picks up hydrogen during normal service, which can lead to cracking in new welds (Figure 3).
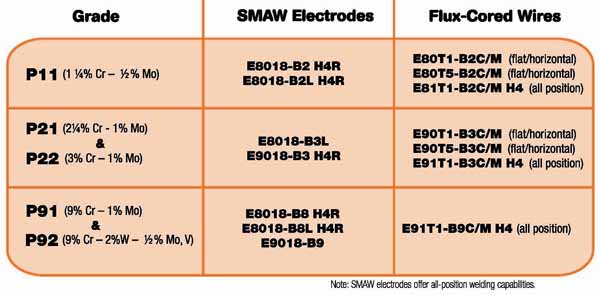
3. Recommended filler metals for welding chrome-moly pipe. Source: Hobart Brothers
For P11 (1¼% Cr – ½% Mo) chrome-moly pipe, use either an AWS E8018-B2 H4R or E8018-B2L H4R SMAW electrode, as both are formulated for applications subject to high heat and/or humidity. They also resist hydrogen pick-up that can lead to cracking or starting porosity. The E8018-B2L H4R stick electrode contains a lower amount of carbon, which further protects against cracking. Both electrodes work especially well on boiler and similar piping repairs that require weld tensile strengths above 80,000 psi. On average they offer tensile strengths in the range of 90,000 to 98,000 psi.
P21 (2¼% Cr – 1% Mo) or P22 (3% Cr – 1% Mo) pipe requires SMAW electrodes with higher chrome content and higher tensile strengths than those used for P11 pipe. Options include AWS E8018-B3L, E9018-B3 H4R, or E9018-B3L H4R electrodes, which are good for boiler work and general piping applications. These SMAW electrodes yield tensile strengths in the range of 105,000 to 110,000 psi and usually feature a special moisture-resistant coating that protects against hydrogen pick-up in service conditions of high humidity or heat.
Finally, when repairing P91 (9% Cr – 1% Mo) or P92 (9% Cr – 2%W – ½% Mo, V) pipe, choose an SMAW electrode formulated to improve creep resistance. Creep is any deformity (buckling, warping, or the like) caused by stress and/or heat during the welding process, and higher-strength chrome-moly is prone to this occurrence. AWS E8018-B8 H4R, E8018-B8L H4R, or E9018-B9 SMAW electrodes can help provide that protection and are good choices for petrochemical or petroleum pipes or other surface applications exceeding service temperatures of 300F. They yield tensile strengths between 100,000 and 110,000 psi.
As with any SMAW electrode, proper storage of low-alloy electrodes is the key to preventing moisture pick-up. Dry, cool areas are ideal. If reconditioning is necessary, follow the filler metal manufacturer’s recommendation for reconditioning temperature and duration.
Don’t Get Flustered
Low-alloy flux-cored wires are typically reserved for fabricating chrome-moly pipe, as opposed to repairing it. There are two primary reasons for this: flux-cored welding is faster in terms of pre-assembly work, where productivity is key, and most low-alloy flux-cored wires are gas-shielded, which makes them much less portable for repairs (they require an external shielding gas tank). Low-alloy flux-cored wires can be used for repairs, but only if the repairs are in an area with sufficient access and the correct equipment is available.
Like low-alloy SMAW electrodes, low-alloy flux-cored wires are designed with fast freezing, easy-to-remove slag, and low hydrogen levels, but they also offer high deposition rates and good weld penetration.
When fabricating P11 chrome-moly pipe, the following flux-cored wires can be used: AWS E80T1-B2C/M, E80T5-B2C/M, and E81T1-B2C/M, all of which offer excellent strength plus creep and corrosion resistance in high service temperature applications. They are comparable in their characteristics to an E8018-B2 SMAW electrode, but they will yield different tensile strengths according to the shielding gas used. A “C” at the end of the AWS classification indicates the wire requires 100% CO2, whereas an “M” indicates the wire uses a 75% argon/25% CO2 mixture and provides higher tensile strengths.
All of the wires are designed for single- or multiple-pass welding; however, the E80T1-B2C/M and E80T5-C/M can only be used in the flat and horizontal positions, which means the chrome-moly pipe will need to be rotated during welding. These flux-cored wires offer a tensile strength of approximately 99,000 psi.
The other wire can be used in all welding positions. An E81T1-B2C wire requires 100% CO2 shielding gas and creates welds with around 96,000 psi tensile strength, whereas the E81T1-B2M uses a 75% argon/25% CO2 mixture and can yield tensile strengths above 100,000 psi. Regardless of the shielding gas or the strength, this type of wire helps resist hydrogen pick-up when the pipes enter into the service environment.
The main low-alloy flux-cored wires for welding P21 and P22 chrome-moly pipe include AWS E90T1-B3C/M and E90T5-B3C/M for flat and horizontal welding, and the E91T1-B3C/M H4 for all-position welding applications. The E91T1-B3C H4 requires 100% CO2; the E91T1-B3M H4 uses 75% argon/25% CO2 shielding gas. Like other low-alloy flux-cored wires, these offer good corrosion and cracking resistance. They are good choices for fabricating pressure piping and steam or chemical pipes requiring strengths over 100,000 psi.
Typically, the best low-alloy flux-cored wire for welding P91 and P92 chrome-moly is an AWS E91T1-B9. This type of wire offers a fast-freezing slag for out-of-position welding, along with low diffusible hydrogen levels to control cracking. It also has a very high tensile strength: approximately 126,000 psi. Not surprisingly, because P91 and P92 chrome-moly pipe are used for higher-temperature services than the other grades, E91T1-B9 flux-cored wire creates x-ray-quality welds, which are essential on such critical piping applications.
Remember, when repairing or fabricating chrome-moly pipe, corrosion-resistant, high-temperature, and high-strength welds are the goal. Each of the low-alloy flux-cored wires (and SMAW electrodes) mentioned here can provide those properties. They can also prevent cracking that could lead to unwanted service conditions.
—Keith Packard (keith.packard@hobartbrothers.com) is product manager, Tubular Wire Division, and Bruce Morrett (bruce.morrett@hobartbrothers.com) is product manager, Stick Electrode Division for Hobart Brothers.