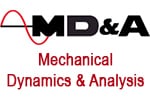
A carefully orchestrated process was set in motion when Mechanical Dynamics & Analysis (MD&A) ventured to complete a 7FA gas turbine hot gas path inspection, together with a 7FH2 generator inspection and repairs providing all services, labor, and parts. Under a tight timeline, MD&A experts were able to complete the work in 19 days.
At MD&A’s Gas Turbine Parts Service Facility in San Antonio, experts removed, cleaned and inspected all combustion and hot gas path components for the gas turbine. This included refurbishing all combustion parts of fuel nozzles, combustion system liners, liner caps, transition pieces, and flow sleeves, while providing all required hardware.
The process revealed that the stage 1 nozzle needed to be replaced with a new assembly. The site team proceeded to replace both the right and left stage 1 forward wheelspace thermocouple guide tube assemblies. The stage 2 and stage 3 nozzle segments were also replaced and new shroud blocks and new installation hardware were provided for all stages. The team identified moderate fretting, which warranted replacement of the exhaust frame flex seals as well.
Simultaneously, MD&A experts removed both turbine-end and collector-end upper half end shields to perform a generator minor inspection consisting of stator and field visual inspections, including in-situ robotic inspections, ELCID, and electrical testing.
The Generator Specialist immediately recognized that the stator had significant connection ring damage that could have led to catastrophic damage had it continued to operate.
The solution: MD&A expeditiously removed, reverse engineered, and replaced the damaged components with no impact to overall outage schedule (5 days total repair time).
Additionally, scoring was identified on both the turbine-end and collector-end journals. The lower half bearings had moderate abrasion/scoring; minor babbit damage was also noted. MD&A found the turbine-end and collector-end hydrogen gas and air side seals were in poor condition and replaced them.
Winders were mobilized to perform numerous tie repairs on each end of the unit and connection ring replacement on the collector end with the rotor still in place. As a result of MD&A’s impact testing and modal analysis, additional blocking and ties were made on the connection rings to ensure the unit will not see this type of problem again.
At project conclusion, the team provided comprehensive reports listing each step of the process and its engineering rationale, along with detailed analysis and long-term predictions and recommendations.
MD&A site and shop repair experts worked closely together to deliver first class service. MD&A’s provides a one-stop shop solution for turbine & generator services, parts, and repairs.
Learn more about this case study and MD&A Gas Turbine Services by calling (518) 399-3616 or through this contact form.
The countdown was set for T-19 days to complete a 7FA gas turbine hot gas path inspection together with a 7FH2 generator inspection and repairs providing all services, labor, and parts. While the average time for such project can be much higher, the Mechanical Dynamics & Analysis (MD&A) team of experts was able to perform a carefully READ MORE
function db_download_file(){
document.write(”);
return true;}
document.write(”);