The 2008 Powder River Basin Coal Users’ Group (PRBCUG) set new records for attendance again this year with more than 400 registered members for the three-and-a-half-day event, 268 of whom were from operating companies. The meeting’s Grand Sponsor was Benetech and its Plant Professionals group.
The meeting began with the Power Plant Awards Banquet on Monday night, prior to the official start of ELECTRIC POWER. More than 200 people enjoyed the evening’s two special events. First was presentation of awards, including the PRBCUG Plant of the Year award (Figure 1) to Luminant’s Big Brown Plant. (An in-depth look at Big Brown begins on page 40.) Awards were followed by an inspiring presentation by astronaut Fred Haise, immortalized by the movie Apollo 13 (Figure 2).

1. Best of class. The PRB Coal Users’ Group 2008 Plant of the Year award went to Luminant’s Big Brown Steam Electric Station for its innovation and the implementation of “best practices and best available technologies.” Accepting the award from Bob Taylor, PRBCUG chairman, were Freeman Jarrell, director of generation, and Allen Riddle, production superintendent. Source: POWER
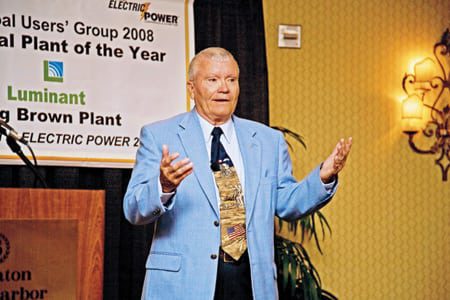
2. Real rocket man. The featured speaker for the Power Plant Awards Banquet was Fred Haise, lunar module pilot for the ill-fated 1970 Apollo 13 space mission. Haise reviewed, with actual flight footage, the events that caused the mission’s moon landing to be scrubbed and the crew’s eventual safe return to Earth. Source: POWER
Who we are
The PRB Coal Users’ Group is dedicated to providing the power industry with essential information required for the safe and efficient handling and burning of Powder River Basin coals. Education is the essential ingredient of a proactive program that safely and effectively manages PRB coal use, and education is the focus of our annual meetings. Sharing experiences, good and bad, improves the industry’s understanding of the peculiarities of burning PRB coal. Our interactive forum gives members the opportunity to discuss PRB issues with their peers and make new friends whom they can call when the next problem unexpectedly appears at their plant.
Chairman Bob Taylor, manager of environmental safety and health at American Electric Power, opened the meeting with a review of the group’s accomplishments last year. One was the overwhelming success of the PRB Coal 101 webinar. (Click on the “Burning PRB Coal?” icon at the bottom of the POWER website: www.powermag.com. The webinar is free.) Another was the number of members active in subcommittees to develop best practices for handling and burning PRB coals.
At our annual meeting, the main meeting is held on the first day, while breakout sessions on coal handling, safety, fire and risk management, and boiler and combustion are held on days two and three. The morning of day four is reserved for generation company members only to hold an open discussion with PRBCUG board members on any issues of interest.
Demand for PRB moves east, and offshore
PRB coal supply challenges have been a hot topic in recent years. Today, power plants burning PRB coal are flush with record high fuel inventories. Mines and railroads are breaking production and shipping records and are on pace to ship nearly 500 million tons out of the Montana and Wyoming PRB mines in 2008.
This year’s panel on PRB coal supply was assembled to discuss the status of transportation and delivery issues. It featured Doug Glass, VP and general manager energy for the Union Pacific (UP) Railway; Tom Canter, executive director, National Coal Transportation Association; Andy Blumenfeld, VP market research for Arch Coal Co.; and Janet Gellici, CEO, American Coal Council.
Glass explained that the overall increase in UP’s efficiencies was thanks to railcar capacities increasing nearly 1,000 pounds per car since 2002 and the billions of dollars spent on track expansions, maintenance, railcars, and locomotives. All those investments were made to stay ahead of demand (Figure 3). Glass also noted that new demand for PRB coals is showing up in the eastern coal markets, where bituminous coals are moving to ocean markets and the price has more than doubled in the past year (Figure 4). PRB coals are also moving to other U.S. shores for export: to the Gulf of Mexico for the European market and the Northwest for the Asian market (Figure 5).
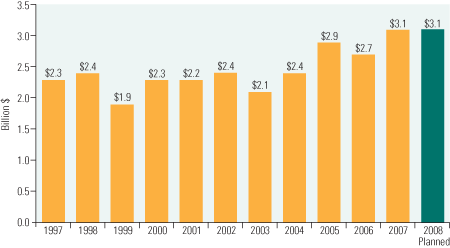
3. Big-buck business. Union Pacific continues record levels of capital investment in 2008 to reduce track congestion on key rail lines even as steel and other commodity prices increase. Source: Union Pacific
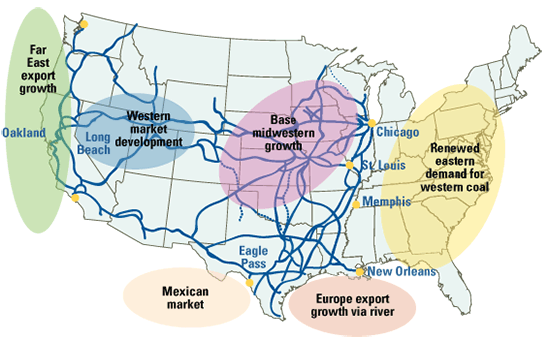
4. PRB coal moves east. Demand for PRB coal continues to increase, and record shipments are expected in 2008. Much of the growth has occurred in the eastern U.S. Source: Union Pacific
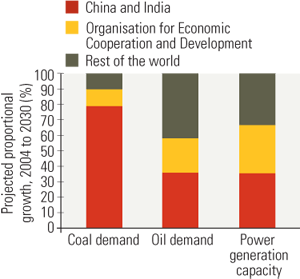
5. Strong overseas energy demand. China and India account for a significant part of the anticipated growth in global fuel demand and power generation capacity between 2004 and 2030. Source: American Coal Council
Canter discussed coal dust ballast fouling issues and the testing being conducted by a consultant hired by the National Coal Transportation Association. The tests consist of eight different companies applying a railcar topper to trains leaving the Powder River Basin region. The trains will be evaluated by dust monitors located at the southern and northern ends of the joint line. Results of the testing are expected to be completed by the end of the year.
Blumenfeld commented that production costs in the Powder River Basin are like all others in today’s economy: increasing. The cost of a large shovel is up over 50% from just over two years ago, and steel prices continue to climb in 2008. Commodity costs also continue to rise: Diesel fuel is up over 90%. Blasting agents are up 20%, emulsion is up 15%, and tires are up 30%—just since 2006. The cost of new leases has also significantly increased: from $0.20 per ton in the early 1990s to nearly $1.00 per ton in 2005. But FOB mine prices are still way below $1.00/ million Btu because mining companies have been resilient over the years in applying the latest technologies to reduce their costs. Stripping ratios have increased from 1:1 to consistently 3:1 or higher, requiring some of the biggest earth-moving machinery in the world (Figure 6).

6. Truck costs rise. Purchase costs for rolling stock have increased significantly over the past two years, as have fuel costs. This mining truck is moving coal at Black Thunder Mine in Wyoming. Courtesy: Arch Coal Inc.
Gellici commented on the eastern coal regions, noting that the Northern Appalachia mines are looking at an increase of 30 million tons by 2015, whereas output from the Central Appalachian region will be declining by 60 million tons in the same period. The Illinois Basin is gearing up for scrubbed units by increasing its coal production by 36 million tons in the next eight years. In 2005 just over 100 GW of capacity were scrubbed; nearly 180 GW are expected to be scrubbed by 2010. Demand for high-priced low-sulfur Central Appalachian coal will diminish along with reserves.
OSHA: A tiger growing teeth
Over the past several years the PRBCUG has been developing best practices and educating the industry in an effort to avoid mandatory regulations regarding combustible dusts. Congress, also recognizing the dangers of fugitive dust, is not waiting for regulators to develop new dust rules.
On April 30 of this year, the House passed the Workers Protection Against Combustible Dust Explosions and Fire Act, H.R.5522, by a vote of 247-165. This act would force the Occupational Safety and Health Administration (OSHA) to issue and enforce mandatory dust regulations in all industrial work areas. The White House has indicated that President Bush will veto the bill because its hasty consideration has not allowed for enough review.
In October 2007, OSHA unveiled its National Emphasis Program (NEP) regarding inspection instructions for facilities with combustible dusts present as a direct result of recent events related to inadequate safeguards and compliance in combustible dust environments. OSHA recently completed training an initial 40 compliance officers for the NEP. It is interesting to note that in the past 20 years, only eight NEPs have been issued. (NEPs are used by governmental agencies to call attention to or focus on existing standards and on instructions pertinent to their enforcement.)
AEP’s Bob Taylor; Mark Collett, VP business development for Plant Professionals, a division of Benetech; Ed Douberly, president of UFPE Group; and Charles Kelley, director of industry human resources issues at Edison Electric Institute sat on a panel that discussed what we should expect from OSHA and its new NEP rules.
A U.S. Chemical Safety Board-conducted Combustible Dust Hazard Study found that, from 1980 to 2005, 119 workers were killed and 718 were injured in dust explosions in industrial settings. Ten percent of those accidents occurred in the power industry, and half were related to the operation of fabric filter dust collectors. As a result, OSHA issued CPL 03-00-006 on October 18, 2007, and reissued CPL 03-00-008—which applies to all carbon/coal dust but excludes grain (Figure 7)—on March 8, 2008.
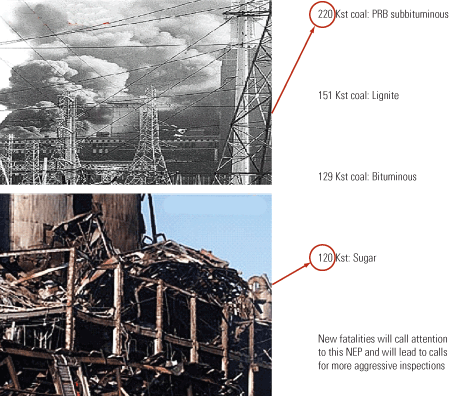
7. OSHA gets some teeth. Recent legislation will give OSHA inspectors increased inspection authority as part of a new National Emphasis Program to reduce dust explosions. OSHA’s emphasis will be to eliminate the hazards and risk associated with combustible dust explosivity (Kst). The higher the Kst, the higher the risk. Courtesy: AEP and Benetech Inc.
The target staffing for this NEP is four compliance safety and health officers (CSHO) per year per OSHA office, and these inspectors will have significant authority in carrying out their duties, unlike current OSHA inspectors. Facility inspections will be random, with no prior notice. Inspectors may go anywhere consistent with health and safety and may enter “without delay” and can obtain a warrant if necessary to enter the property. They will also have full access to employees, managers, and contractors on site. They can require testimony under oath, speak with individuals privately, have a bargaining unit employee representative present on the walk-through, and they will carry a camera or video recorder. After the opening conference with the plant and preliminary walk-through, the CSHO can expand the inspection or terminate it.
Inspectors will have the authority to review a plant’s history of fires, events, and injuries; area classification discussion; drawings; and National Fire Protection Association Emergency Action Plan. You should also expect the inspector to request details of your ignition control program, including hot work permit process, explosion venting calculations, combustible dust-warning signs, and safety and health manuals or other records.
OSHA will also review the designed airflow velocities in ducts and collectors to ensure that velocities are adequate to entrain the dust and prevent dust accumulations. The plant’s housekeeping program must include regular cleaning frequencies for floor and horizontal surfaces and training to sustain “OSHA READY” preparation.
Inspectors will be authorized to issue citations that cover a wide range of plant operations and administrative functions, including these:
- Housekeeping and accumulations. Coal dust >1/19” thickness (0.052”) over 5% of the surface area or 1,000 ft2, whichever is less.
- Ventilation and deflagration isolation. Dry dust collectors (>8 ft3 internal volume) that are improperly designed or maintained (where new fuel does match design, for example), have inadequate spark prevention/detection, have improper deflagration venting design and inadequate vent sizing to protect employees, are located inside buildings or returning air to the inside of buildings, or are in inhabited areas in the path of explosion venting are subject to citation. Also, mills not protected by inerting systems, flame arrestors, flame front diverters, or spark detection can be cited.
- Administrative responsibilities. Plants are expected to keep their manuals, instructions, preparedness instructions, employee training requirements, and other “standard” safety and health issues up to date.
Failure to keep a program up to date will result in significant penalties. Willful violations, where an employer intentionally and knowingly commits a violation, result in a mandatory penalty of $5,000 to $70,000; where a violation results in death, penalties of imprisonment (up to six months) and fines up to $250,000 for individuals and/or $500,000 for an organization will result. For serious violations, a mandatory $7,000 per violation will be assessed; violations other than serious ones will incur a discretionary civil penalty of $7,000 per violation. A repeated violation of any standard, rule, or order where, upon re-inspection a similar violation is found, will result in a $70,000 penalty. A penalty of $70,000 will be assessed for every day beyond the abatement date per violation.
Congress and OSHA are very serious when it comes to combustible dusts. Coal-burning electric utilities need to be proactive in addressing this issue at their plants. Already, two utilities have experienced an OSHA NEP inspection under the new guidelines. The results were not favorable for these utilities.
Coal-handling life-cycle changes
In 2003, Westar Energy’s Jeffrey Energy Center (JEC) was the PRBCUG Plant of the Year. JEC continues to demonstrate leadership in the industry by strategic investment in new technologies and enhancements to the plant’s existing coal-handling system. In another session, Troy Mussetter, operations superintendent at JEC, and Pete Zinecker, area manager for Benetech, presented JEC’s continuous improvement process and investment strategies.
Mussetter said that in 2006, JEC committed to implementing a comprehensive safety and health management program—the OSHA Voluntary Protection Program (VPP)—and ultimately gained VPP “STAR” status in March 2007. The VPP program was discussed, funded, and implemented to achieve the goal of having more people go home safe. JEC’s incident rates are continuing to improve: from 23 recordable incidents in 1997 to five recordable incidents in 2007. Westar’s corporate goal is zero today and zero tomorrow. Additional benefits of the VPP include increased profitability due to a reduction of injuries, lost time, and workers compensation, as well as increased cooperation between labor and management on safety-related issues.
Many of the upgrade projects completed by JEC focused on PRB coal-handling improvements, such as:
- An independent third-party risk assessment and five-year plan that assessed the current and future needs of the coal-handling system defined by probability, life span, and safety concerns.
- The replacement of four original 30-year-old chutes with new, distinct-style engineered chutes. The two 4,000-tph and two 1,500-tph chutes are “smart” chutes, utilizing patented technology to reduce velocity on impact. Benefits gained are increased belt life, improved safety profile, reduce dust and spillage levels due to the reduced force of impact, and eliminating the need for skirt boards or expensive skirt rubber.
- A dust suppression program was implemented on the dumper feeders and in two transfer houses to enable the plant to reduce opacity levels during stackout and reclaim. The vendor provides complete system maintenance, reporting, and testing.
- The fire protection system was upgraded with new valves, nozzles, thermal detection wire, and chemical bladders.
- Idler/roller catch trays were installed on return rollers on elevated conveyors over existing personnel and travel areas.
- Housekeeping changes were implemented with the addition of more contract labor for washdown and cleanup. The changes mean work flow is not interrupted by operational necessity (operators can be operators), and washdown and cleanup can occur on a regular cycle based on an effective plan.
Other investments made by JEC were to improve plant safety as part of its VPP certification process, including these:
- Protection for rotating element pinch points.
- Guarding conveyor tail pulleys.
- Upgrading of the lockout/tagout program, controls, and responsibility.
- A significant increase in employee safety training.
- Corporate-driven internal safety audits to continually assess the VPP results.
Maintaining the rolling stock
Harry Mullins, manager railcar maintenance for Southern Company, and Larry Rose, manager of operations and logistics fuel supply for DTE, led a session describing their companies’ railcar maintenance experiences. Interest in this session was unexpectedly high; Mullins and Rose fielded questions from the audience long after the last session of the day was over.
Southern Company has approximately 160,000 aluminum rapid-discharge coal cars in train sets ranging from 70 to 135 cars. Mullins said his company’s objectives were to reduce the number of bad orders (bad railcars) on the railroads, keep the trains in complete sets with the maximum number of cars when they arrive to be loaded, reduce the number of problems at the customers’ sites, and run railcars through the shop for maintenance twice a year.
Mullins stressed several times during his presentation, and in his remarks afterward, that in order to have the best chance of reaching the company’s objectives, all parties must work together as partners. That partnership includes producers, shippers, maintenance shops, railroads, and third-party unloading crews. If the railcars are properly maintained and bad-order cars are minimal, the system will work much more efficiently. No party benefits when a railcar is set off as a bad order and the train runs short of the minimum number of railcars.
Conveyor belting 101
A new session on conveyer belts was added this year in response to the large number of requests made on the conference evaluation forms filled out the previous year. The PRBCUG asked Mark Alspaugh, president of Overland Conveyor Inc., to present this session and to host a preconference workshop on conveyors and belting. Conveyor belt performance and life remain a concern, even though new computer design technologies that assist in the design of conveyor systems, such as Overland Conveyor’s Belt Analyst program, are now available.
Conveyor belts are the single largest contributor to dust generated in a fuel-handling system, so selecting the appropriate type of conveyor belt is critical to proper operation of a conveyor. PRB coals are hydroscopic and leach the plastizers out of the belt’s top cover, making coal loading of the more-brittle surface problematic. Surface cracks hold dust, and this dust is released along the return side of the conveyor and when the belt goes around pulleys. Consequently, selecting the proper rubber compound for the top cover is critical to getting the full life out of a belt.
Alspaugh outlined 10 steps for selecting the proper belt design for your application that should result in increased life and performance of conveyor belts and decreased operating costs:
- Carefully select the carcass (weave and number of plies) and cover (rubber grade and gauge).
- Ask: Why do you need a belt? How long did the previous one last?
- Know your application. Have calculations performed by the belt supplier.
- Before buying, write a specification that includes a test method, nominal performance, and tolerance.
- When installing, realign the structure; define the splicing process, including splice design, materials, and temperature/pressure; and train technicians.
- Check your conveyor, especially pulleys, idlers, transitions, and vertical curves.
- Check the belt during loading and starting.
- Remember to do housekeeping, lubrication, and belt tracking.
- To troubleshoot, use root cause failure analysis to determine what, how, and why something happened. The four majors steps are data collection; chart, organize, and analyze the data; root cause identification; and recommendation generation.
- Look at the life-cycle cost. The lowest purchase price does not always deliver the lowest cost.
—Randy Rahm (rrahm1@cox.net) is president of CoalTech Consultants Inc., former chairman of the PRBCUG, and a POWER contributing editor.
Join us in Chicago in 2009
There were many suggestions from members for subjects to cover at the 2009 PRBCUG meeting in Chicago. Suggested topics included world coal supply and demand, how to cope with cultural changes, round two from Richard Storm on mill performance, more details and updates on the OSHA NEP, railcar maintenance with Harry Mullins and Larry Rose, blending case histories, the conversion process, thermal imaging techniques and procedures, Mark Alspaugh presenting Conveyor 201, and much more.
Whatever the final lineup, the 2009 meeting will educate your plant staff on safety issues and industry best practices for the handling and storage of PRB coals. We look forward to seeing you May 12 to 14 in Chicago for the 9th annual PRB Coal Users’ Group Meeting, colocated with the ELECTRIC POWER Conference. More information is available at www.prbcoals.com.