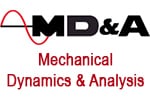
Mechanical Dynamics & Analysis (MD&A) performed a complete reheat stop valves restoration along with one LP stop valve. These RH stop valves on a Siemens Westinghouse® unit had not been fully restored for 14 years.
Pre-outage planning took place between our team and key plant personnel. Upgraded valve materials were designed and manufactured, and new clearances were specified and reviewed. For the RH stop valves, the customer wanted material upgrades to extend the length between valve outages, and to inhibit blue blush (thin, heat-induced oxidation layer) buildup during outages.
While on-site, MD&A was also contracted to assist the overhaul of the LP and HP turbines, accompanied by removing the valve sub-assemblies. Site work was completed within a 30-day outage.
After disassembly, key components were shipped to MD&A’s Valve shop in St. Louis for reconditioning, evaluation of diametrical clearances, and materials upgrades. Components shipped included:
- Outer bearing cover
- Reheat shaft
- Cylinder support yoke (mummy case)
- Actuators
- Flapper arm / Disc assemblies
- Valve casing covers
The new valve components from MD&A’s Parts Division were received at MD&A’s St. Louis Repairs Division Valve shop.
Casing components were restored on-site, including:
- Cover flange gasket pocket (machined to accept a new Flexatallic® gasket)
- Cylinder support yoke and end bearing cover studs, removed and cleaned for reuse
- Replacement of all spherical washers
- Diametrical and axial inspection of both valve casings, including passing a 100% blue contact check
MD&A experts machined the cylinder support yoke and end bearing cover fit bores, and bolt faces to minimum cleanup. A lap was manufactured and the seat contact face was lapped perpendicular to the shaft bores to restore the seating surface.
All bushings were upgraded to 422SS material with nitride coating. The new shafts were 901 Nemonic.
Furthermore, these valves had always used a soft metal gasket for sealing of the cover on top of the casing. The customer wanted to upgrade to a Flexatallic® design with a specific crush dimension for improved sealing. The gasket pocket was increased in depth from 0.250 inches to 0.312 inches to accept the new gasket. The bolt face was machined to minimum cleanup, and the cover was sent to St. Louis where the gasket mating surface was machined to a proper thickness.
While on site, localized weld repairs were made to the blade rings and horizontal joint. MD&A welding experts examined all rows of the HP turbine and straightened all blades that had been subjected to foreign object damage during operation. All nozzle partitions were blended, polished, and cut back as necessary. Main oil pump seal faces were also reconditioned, and new seal rings were manufactured. Main steam seal rings were repaired, and all inlet flanges were restored to OEM conditions.
As part of this project, a low-pressure stop valve was also checked and returned to OEM design specifications.
Explicit and clearly defined cautions and options were recorded for future outages, including the seat contact work. The recommendations issued as part of the report went well beyond standard recommendations, giving both detail and rationale from MD&A’s unique knowledge and experience.
Although the work scope grew, the MD&A team improved upon the contracted schedule.
MD&A provides inspection, repair, restoration, and upgrades of industrial and utility high-pressure valves and valve components. We offer full-service, one-stop valve repair while delivering consistent quality and value with fast response, superior communications, and innovative solutions.
Check out our video: Full-Service Valve Capabilities Video
Have MD&A look at your valves today, call our Turbine-Generator Repair Facility at (314) 880-3000 or use our Contact form.