Polyalkylene glycol (PAG) and polyalphaolefin (PAO) are two synthetic lubricant options for industrial applications. Understanding the advantages and disadvantages of each can help end-users decide which option is best for a given application.
Why Synthetic Lubricants?
According to analysis conducted by Kline & Co., more than 78% of all lubricant requirements in the world annually are met with the use of mineral oil-based fluids. The use of mineral oil-based lubricants in the world, however, is decreasing. The use of synthetic or “man-made” lubricants in various industrial and automotive applications are becoming commonplace and continues to expand into applications where only mineral oil-based fluids had been used. Reasons to change from mineral oil-based lubricants to synthetics despite the increase in cost include:
- Need fill-for-life lubricant.
- Extend fluid changeout intervals.
- Extend equipment life.
- Meet new original equipment manufacturer and industry standard requirements.
- Meet additional regulations (fire-resistance, environmental acceptability).
- Address specific system site conditions (potential for water ingression).
- Address new equipment conditions (higher operating temperature and pressure, greater loads and speed).
Advances in equipment technology have resulted in more demanding lubricant conditions and requirements, many beyond the capabilities of mineral oil-based lubricants. Synthetic lubricants can meet these demands because they perform better than mineral oil-based lubricants in many or all the critical performance areas: reduced wear and friction, resistance to sludge formation, lower volatility, greater corrosion protection, and improved thermal and oxidative stability.
However, not all synthetic lubricants are created equal. There are multiple formulations behind the science of synthetic lubricants that can complicate making the right choice for any application. Recent advancements in additive technology and synthetic base fluid manufacturing are pushing the performance edges that make current lubricant offerings better than ever.
End-users must first select a lubricant based upon its intended application, such as engine oil, transmission oil, hydraulic oil, wire rope lubricant, electric motor grease, etc. To correctly identify what type of fluid is needed, the end-user must know the minimum lubricant requirements for that piece of equipment. These requirements or specifications will generally identify or recommend a product type (mineral oils, synthetic fluids, or bio-based fluids) and the proper performance requirements (developed into the lubricant by the component chemistry) to allow the machinery to run at an optimum level. This article will discuss the most common synthetic fluids aiming to help end-users make the right choice for their applications.
Types of Synthetic Lubricants
Approximately 80% of synthetic lubricants used in the world are of three types. In order of volume used, they are: polyalphaolefins (PAOs), organic esters, and polyglycols. The remaining synthetic lubricants are produced from other basestocks, including phosphate esters, polybutenes, silicones, perfluoroalkyl, and polyphenyl ethers.
There are multiple considerations when determining the best synthetic lubricant for a particular application, but knowledge of the general properties of the synthetic lubricant types being considered is the starting point. Synthetic lubricants can be very different chemically and what defines those differences are the basestocks used as the basis for the lubricant.
Synthetic basestocks, more so than in mineral oil basestocks, are the primary contributor to most of the basic properties of the lubricant, including oil or water solubility, low-temperature fluidity, lubrication, volatility, ignitability, and seal and paint compatibility. Two major types of synthetic basestocks—polyalkylene glycols (PAG) and polyalphaolefin (PAO)—and the lubricants formulated from them, will be compared.
Polyalkylene Glycols (PAGs)
PAG polymers, first discovered more than 150 years ago, saw their breakthrough application occur during World War ll. At that time, both fires on U.S. Navy ships and aircraft were occurring due to the use of mineral oil-based hydraulic fluids. Research at the U.S. Naval Research Laboratory (USNRL) was begun to develop hydraulic fluids that would be more fire-resistant than the ones used at the time based on mineral oil.
Working in conjunction with the Union Carbide Chemicals, Plastics Company Inc., and the Mellon Institute of Industrial Research, the USNRL developed the first water-glycol, PAG-thickened, fire-resistant hydraulic fluid (WGHF). Use of WGHFs increased tremendously due to the publication of the “Luxembourg Report” in 1961, outlining minimum standards for hydraulic fluid fire-resistance in European coal mines. Use of PAG-based fluids and lubricants began to extend to other applications, first to quenchants and textile lubricants, then to many other lubricant categories, including anhydrous fire-resistant fluids, gear, compressor, and turbine fluids.
How PAG Basestocks Are Manufactured
PAG basestocks are synthetic polymers manufactured using a polymerization process that combines monomers ethylene oxide (EO), propylene oxide (PO), and butylene oxide (BO) singly as homopolymers or in combinations to form a growing chain from a nucleophilic starter molecule, commonly an alcohol. PAG lubricant basestocks can be designed to be water-soluble, water-insoluble (partial mineral oil compatibility), or oil-soluble, depending on the selection of starter molecules and monomers to be used in producing the polymer. The more EO monomer in the basestock, the more water-soluble; the more PO monomer, the more water-insoluble; and the more BO monomer, the more oil-soluble the basestock is. This process creates a polymer backbone where oxygen is every third atom, which gives PAG basestocks their distinctive chemical attributes and allows formulators to synthesize various combinations of starters and monomers (block, random, and homopolymer) to create custom basestock types for specific applications.
PAG basestocks are classified as a Group V oil, meaning a synthetic basestock that is not defined as a Group I, II, III, or IV base oil. Group V oils also include esters and naphthenic oils. PAG-based lubricants are commonly used in compressors, gearboxes, air conditioning systems, metalworking, quenching, and hydraulic systems where fire-resistance or environmental acceptability are required. General properties of water-soluble, water-insoluble, and oil-soluble PAG basestocks are shown in Table 1.
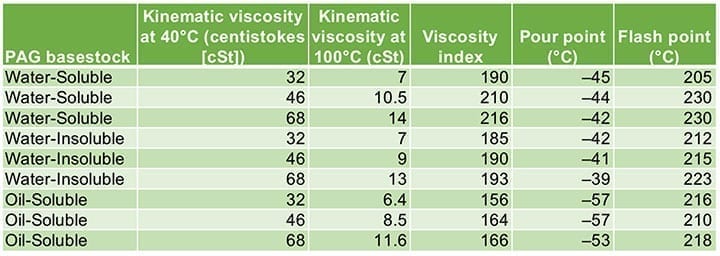
Advantages of PAG-Based Lubricants
PAG-based lubricants provide many property and performance advantages over mineral oil-based and other synthetic lubricants, as outlined in Table 2. The degree of the advantage may depend on the specific PAG basestock type used (such as water-soluble, oil-soluble, etc.).
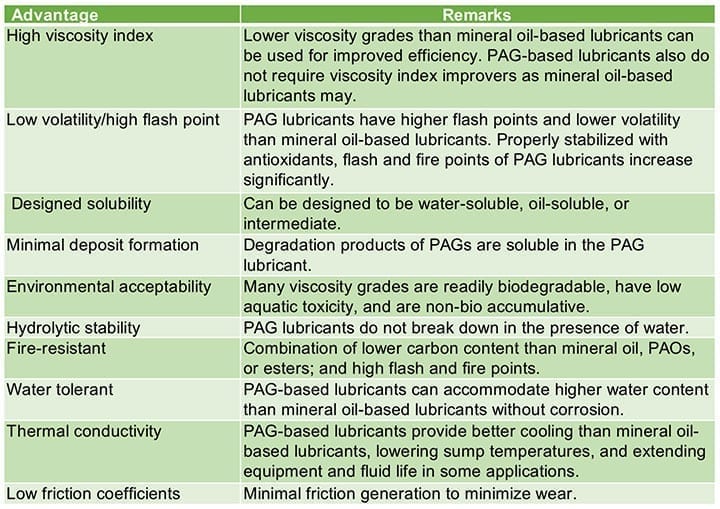
Disadvantages of PAG-Based Lubricants
Lack of mineral oil solubility is a barrier to expanded use of PAG-based lubricants. Due to this incompatibility with many but not all PAG lubricants, system change-outs from mineral oil to PAG-based lubricants may be costlier and take additional time. The degree of the disadvantage for seal and paint compatibility may depend on the specific PAG basestock type used (such as water-soluble, oil-soluble, etc.). When possible, testing compatibility between the specific PAG lubricant to be used and the specific seal types or paints to be used is recommended. Disadvantages of PAG-based lubricants are summarized in Table 3.
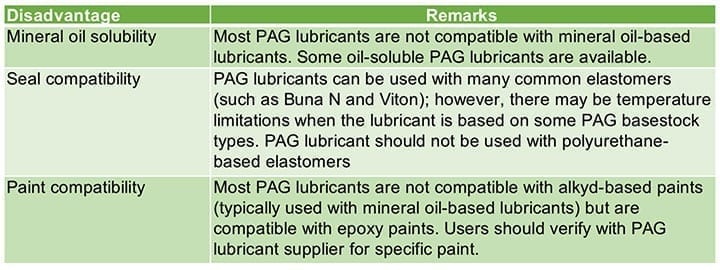
Polyalphaolefins (PAOs)
PAOs are the most common synthetic basestock used in industrial and automotive lubricants. It is a synthetic hydrocarbon (SHC) that mimics the best hydrocarbon (branched, non-ring) structure found in mineral oils and so corrects for many disadvantages of using mineral oil lubricants, including poor low-temperature fluidity, poor viscosity index, sludge deposits, and high volatility.
PAO basestocks were developed in the 1930s and used commercially as a base for engine oils starting in the 1970s. Applications for PAO-based lubricants expanded to circulating and gear oils. Later used in many industrial applications from compressor, hydraulic, and turbine fluids to gear oils and metalworking fluids.
How PAO Basestocks Are Manufactured
PAO fluids are classified as a Group IV base oil and are made by a two-step reaction process using linear alpha-olefins like 1-decene. The first step is the synthesis of oligomers (polymers with few repeating monomer units) from the linear alpha-olefin. The second step is the hydrogenation of the remaining double bonds (unsaturation) in the oligomer and subsequent distillation to separate the unreacted monomer and light-viscosity grade PAO.
Unlike other industrial basestocks, PAOs are generally classified by their kinematic viscosity at 100°C. PAO basestocks using conventional catalysts are commercially produced in five low-viscosity grades and two high-viscosity grades to a maximum viscosity of 100 centistokes (cSt) at 100°C.
Low-viscosity PAO fluids are used in automotive applications, such as engine oil and gear lubricants. High-viscosity PAO fluids have also become popular in industrial fluids and greases. Since PAO fluids are synthetic hydrocarbons, they are compatible with and often combined with mineral-based oils. Metallocene-catalyzed commercial mPAO basestock grades can attain a viscosity of 300 cSt at 100°C. More uniform in structure than conventional PAO basestocks, they provide similar advantages of high viscosity indices, excellent low-temperature fluidity, and shear stability but with additional thickening ability. General properties of low- and high-viscosity conventional PAO, and metallocene-catalyzed mPAO basestocks, are shown in Table 4.
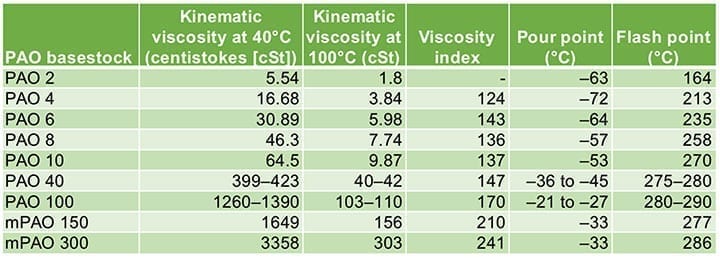
Advantages of PAO-Based Lubricants
Some of the advantages of PAO-based lubricants are summarized in Table 5.
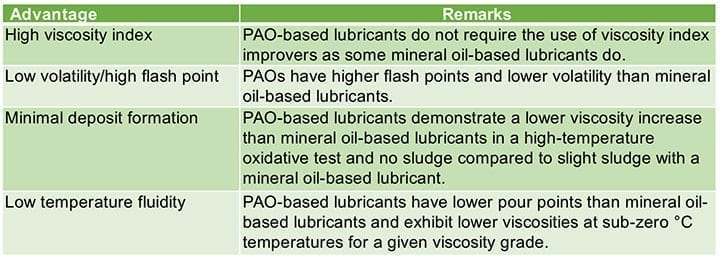
Disadvantages of PAO-Based Lubricants
Some of the disadvantages of PAO-based lubricants are outlined in Table 6.
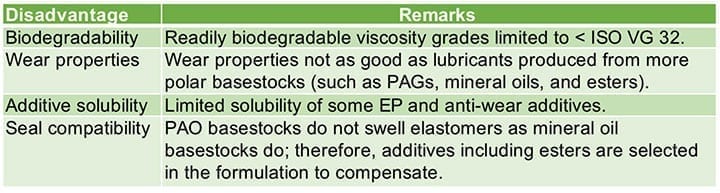
Differences Between PAG- and PAO-Based Lubricants
PAG- and PAO-based lubricants are used in multiple industries and, as synthetics, offer improved performance over mineral oils. Both lubricant types are used in industrial gearboxes, compressors, and even air conditioning systems. However, PAGs and PAOs are two totally different chemical types of synthetic base stocks. They have different characteristics, meaning that one may be superior to the other under certain circumstances.
PAG-based lubricants are polar (water-soluble PAG > water-insoluble PAG > oil-soluble PAG), where PAO-based lubricants are essentially non-polar. This difference in polarity impacts many lubricant properties including elastomer compatibility, paint solvency, deposit control, and lubrication. To improve seal compatibility of PAO-based lubricants, an ester is added to the formulation to add some polarity. The more similar in polarity the lubricants are, the more similar they will behave in the properties mentioned.
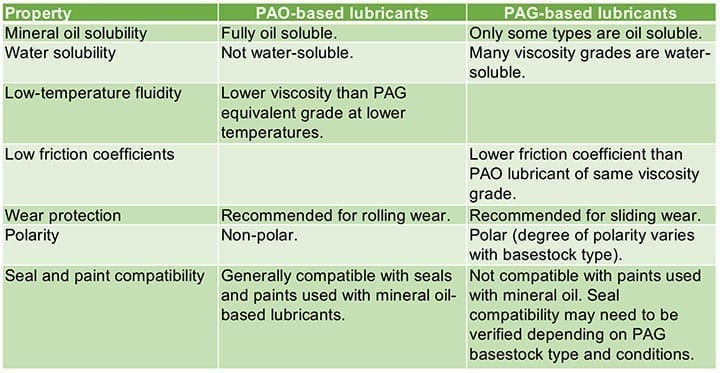
Similarities Between PAG- and PAO-Based Lubricants
PAO- and PAG-based lubricants are both hydrolytically stable and have low pour points. PAO-based lubricants have good viscosity indices superior to lubricants based on Group I, II, and III basestocks of similar viscosity (without the addition of a viscosity improver). PAG-based lubricants have excellent viscosity indices significantly better than PAO-based lubricants of the same viscosity grade. Both basestock types have low volatility and high fire points (when stabilized) for a given viscosity grade.
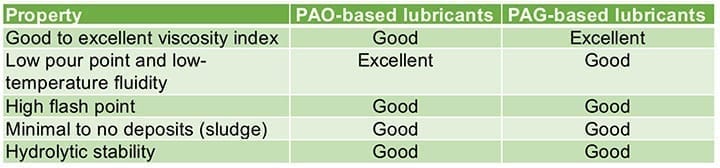
PAG- and PAO-Based Lubricants—Which to Choose?
PAG- and PAO-based lubricants rarely compete in industrial applications. The properties, advantages, and disadvantages reviewed provide some of the main reasons why. Each lubricant type will be the best choice for different sets of use parameters, including:
- Technical and regulatory requirements.
- Equipment and site conditions.
- Level of maintenance and labor available.
- End-user preferences.
PAO-based lubricants may be preferred when the following lubricant attributes are targeted:
- Fill-for-life lubricant.
- Less downtime.
- Fully mineral oil soluble.
- Minimal change-out time and cost.
- Compatible with seals and paint used with mineral oil, no need for change at all operating temperatures.
- No environmental issues.
- No potential for water ingression.
- Fire resistance not required.
- Reduce or eliminate equipment deposits.
- Improved lubrication for rolling wear.
PAG-based lubricants may be preferred when the following lubricant attributes are targeted:
- Fill-for-life lubricant.
- Less downtime.
- Environmentally acceptability.
- Fire-resistance.
- Improved equipment efficiency and energy savings.
- Water ingression possible.
- Reduce or eliminate equipment deposits.
- Improved lubrication for sliding wear.
If end-users are in doubt about which lubricant would best suit their needs, it is recommended that an expert be contacted to assist with the decision-making process.
—John Sherman is Shell Project Lead PAG Lubricant Technology, Industrial Oils and Tech Services; Robert Profilet is Technology Manager, Industrial Lubricants; Warren Cates is Shell Senior Researcher, Industrial Oils and Tech Services; Iris Song is Shell Engineer, Industrial Oils and Tech Services; and Sameer Sathaye is Shell Project Leader Industrial Oils, Industrial Oils and Tech Services.